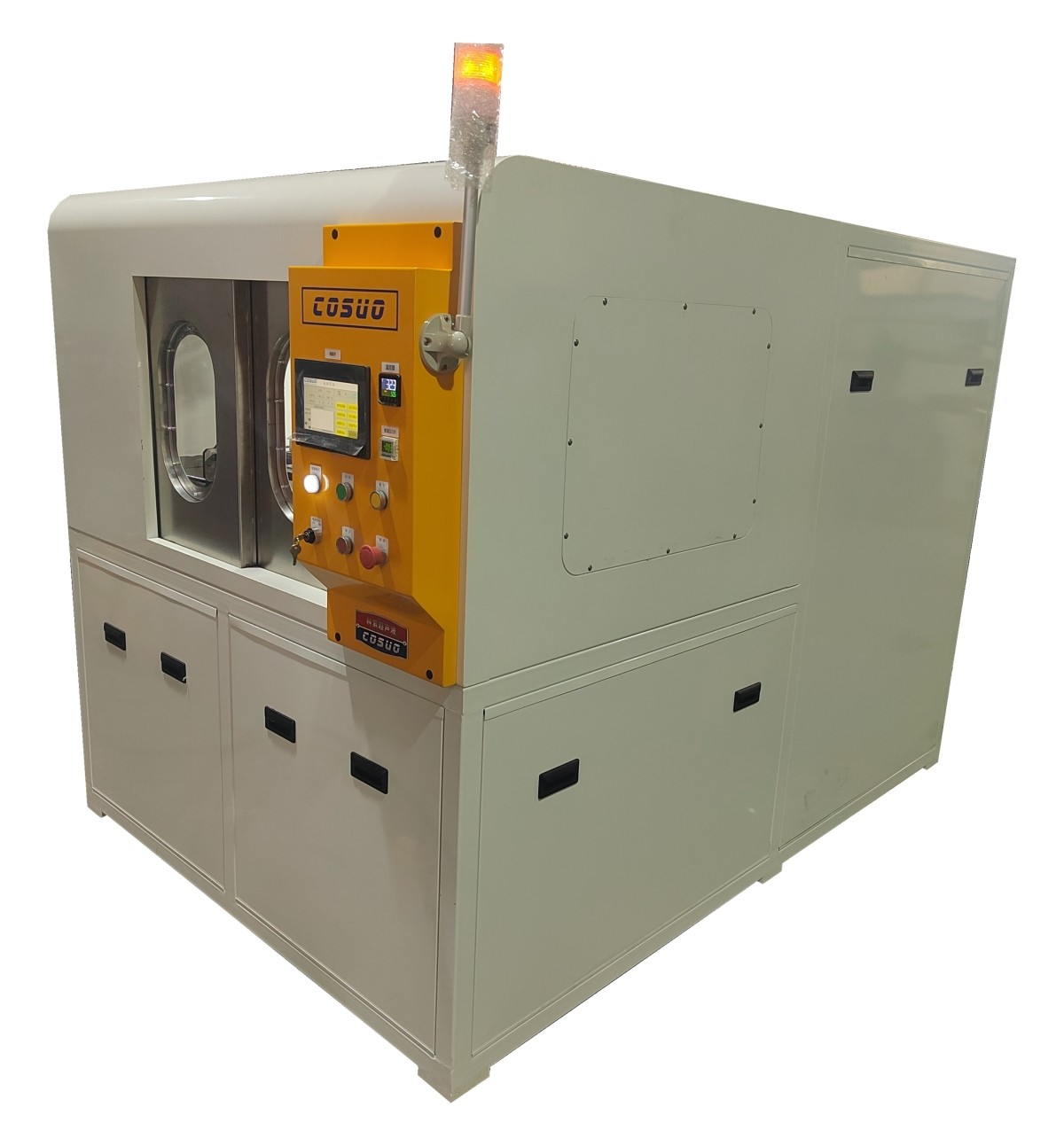
1、 Function description:
After placing the workpiece into the fixture frame, the operator positions the workpiece with the nylon block on the side, presses the start button, and the automatic pneumatic door is closed. Firstly, spray cleaning+swing and immersion turbulent flow cleaning are used. After the liquid is discharged and cut by air, the scanning cleaning and cutting water are driven by the rodless cylinder to scan the workpiece through the spray pipe/cutting air pipe throughout the entire cleaning process. The purpose is to reduce energy consumption and increase the cleaning/cutting water area, so that the workpiece can be thoroughly cleaned and dried. Then manually discharge the material.
2、 Cleaning requirements:
1. The clamping should not damage the machining surface of the parts, and the parts should not deform. There should be no residual water droplets when the parts come out of the equipment, and there should be no obvious water stains on the surface of the parts
2. Cleaning medium: Pure water
3. Cleaning cycle: 8min/basket (adjustable)/8 pieces cleaned each time
3、 Equipment process flow:
Manual loading and unloading - Scanning spray cleaning - Turbulent cleaning with liquid injection in the warehouse - Air cutting and drying/compressed air drying in the warehouse - Manual unloading
4、 Basic structure:
1. Framework structure: The whole machine is a fully enclosed structure
2. Frame material: The chassis and frame are welded with A3 square pipe profiles, and the surface is treated with powder coating
3. Sealing plate material: using T=1.5mm thick A3 plate bent and welded, with surface powder coating treatment

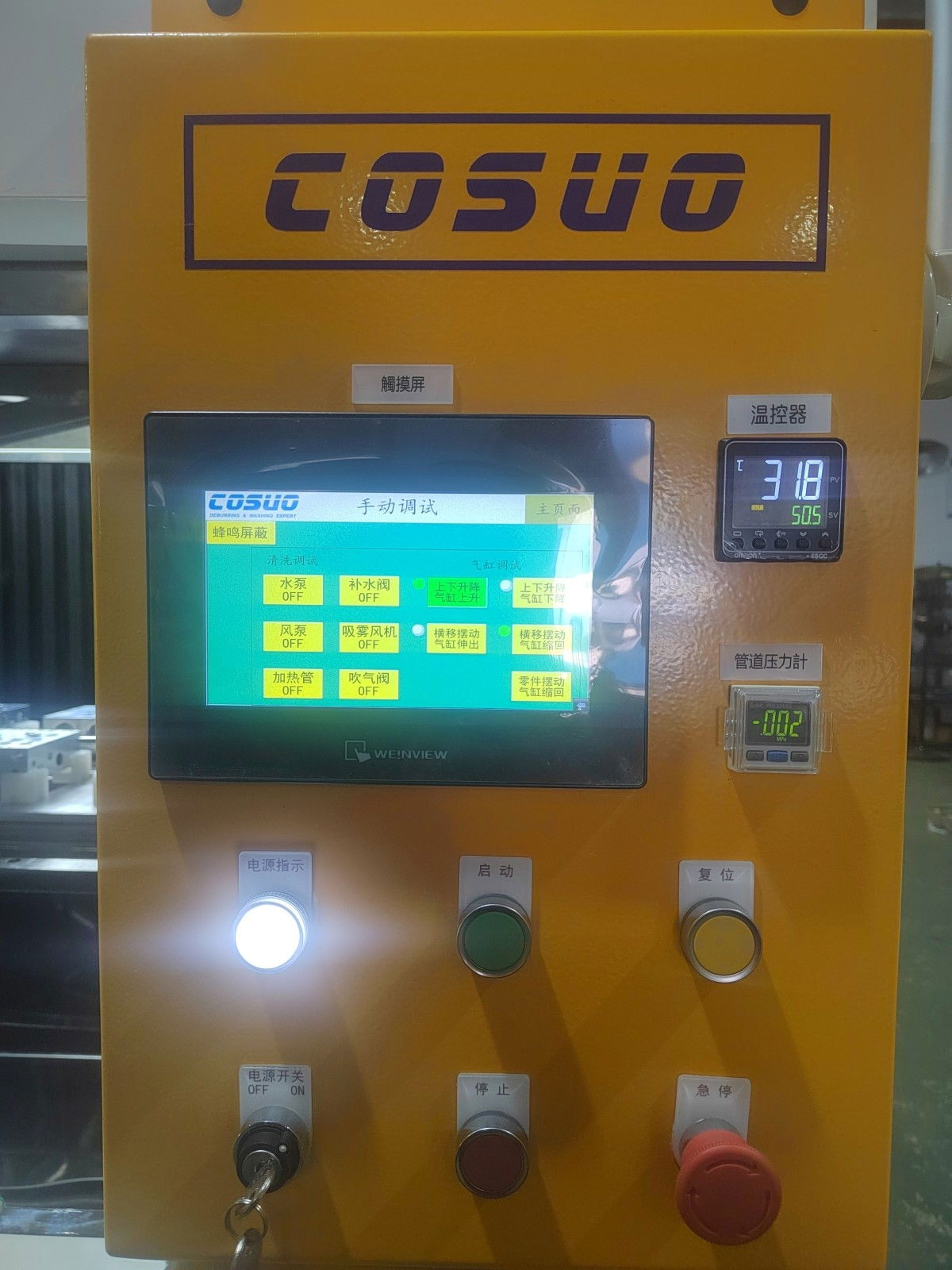

5、 Introduction to Cleaning System:
Cleaning system
1. The cleaning and rinsing systems are composed of "Southern" pumps, "Biyun" bag filters, adjustable quick release nozzles, stainless steel pipelines, ball valves, pressure gauges, etc.
2. The cleaning work pressure is 8 bar.
3. Stainless steel adjustable fan-shaped nozzles are used, with spray pipes arranged in four directions on the workpiece: up, down, left, and right. The cleaning frame micro moves to clean the workpiece in all directions to ensure high cleanliness. The nozzles can be quickly replaced, disassembled, and have adjustable directions.
Filtering system
4. The filtration system of this cleaning equipment adopts two-stage filtration.
5. The first level cleaning liquid storage tank adopts a stainless steel bag filter with a filtration accuracy of 50u, which is manually replaced regularly or alarmed according to pressure
6. The secondary cleaning liquid storage tank adopts a stainless steel bag filter with a cleaning filtration accuracy of 20 μ. It is manually replaced regularly or alarmed according to pressure.
7. The equipment has a blockage alarm function. Equipped with an automatic pressure detection switch device.
Vortex air pump cuts water
8. Use a 7.5kw high flow air pump to cut water from the workpiece. Use a comb shaped air nozzle to fully cover the surface and pores of the part, and cut away any remaining water under high pressure.
Compressed air water blowing system
9. The water blowing system consists of filters, control valves, pipelines, air nozzles, pressure gauges, etc.
10. All air source interfaces are connected with air filters, water separators, and pressure regulators.
11. For the deep holes with steps on the valve body 1 workpiece, the remaining cleaning solution cannot be blown out by the air pump cutting water. Therefore, for the two deep holes of the workpiece, high-pressure drying with fixed-point positioning is used.
Swing mechanism
12.32 * 40 cylinder, adjust the angle of the fixture plate through connecting rod and floating joint
13. Circumstance: about ± 8 °, the workpiece swings with the angle of the fixture plate.
6、 Control system:
1. Cabinet material: A3 board welding, powder coating treatment
2. Power supply 380V, 3-phase 5-wire, operation control circuit DC24V
3. Use a Mitsubishi PLC programmable controller to control the entire operation process, which can be fully self operated or manually operated. Each liquid level controller is connected to the PLC to control fluid replenishment, heating, and pumping. In case of abnormal situations, emergency shutdown is achieved, and sound and light alarms are set up
4. Install emergency stop buttons and alarm devices at both ends
5. Set the operation level for disk making and set parameters based on the permissions of each department
6. Using the "Weilun Tong" brand human-machine interface control, the status of all pumps, motors, heating, liquid level, and translation systems is displayed on the human-machine interface. The control cabinet is integrated with the machine, which does not occupy space and is aesthetically pleasing. The circuit is divided into functional blocks, strong and weak electrical blocks, for maintenance purposes
7. All wiring uses terminal connections.
8. Equipped with clear indicator lights to display the operation of the equipment, A、 Green light: equipment is running normally B. Yellow light: equipment is idle or other C. Red light: equipment is abnormal or faulty

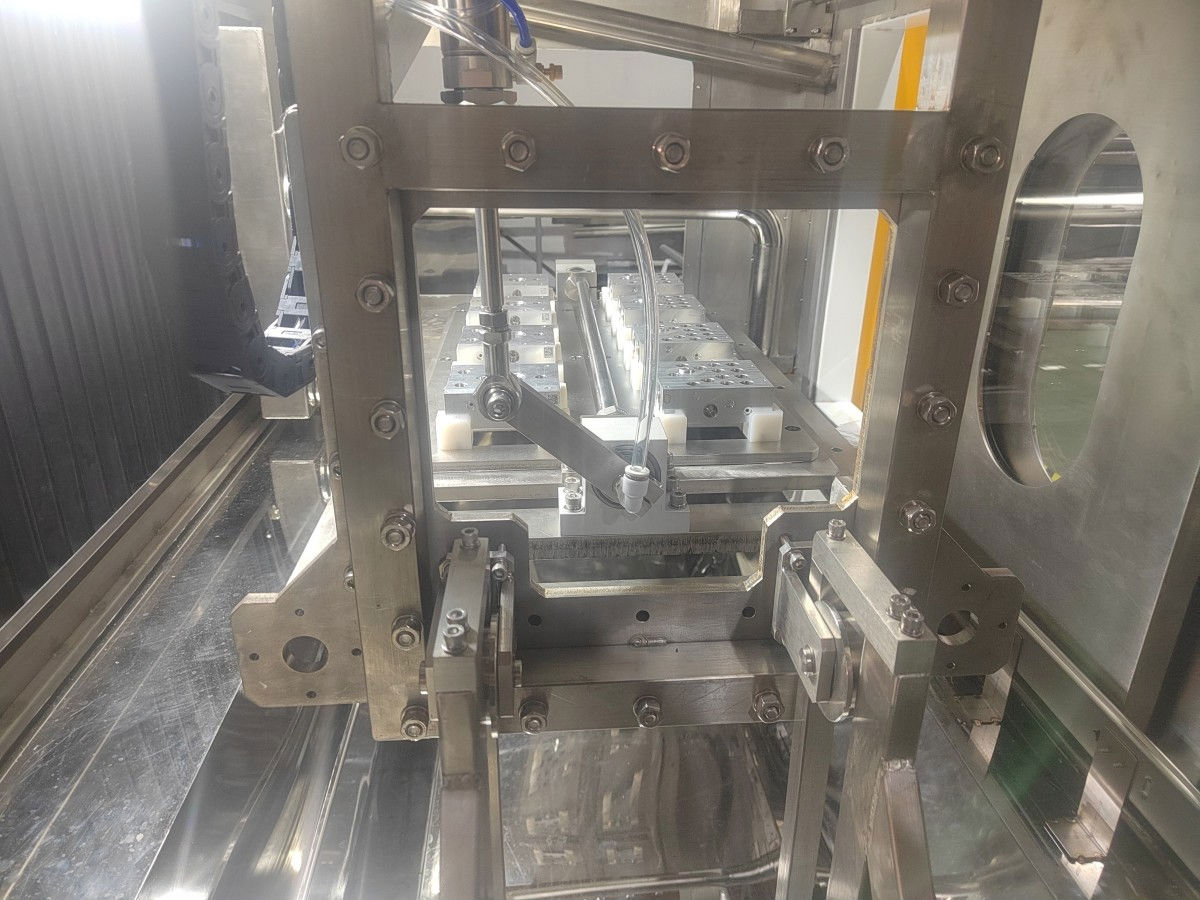
7、 List of Main Purchased Parts:
Number Name Brand
1. Spray pump: Southern vertical multi-stage centrifugal pump
2. Stainless steel heater: customized by Kesuo
3. Cylinder: Japanese "SMC"
4. Electromagnetic valve: Japanese "SMC"
5. Pneumatic valve: Shanghai Juliang
6. High pressure fan: full air
7. Steam recovery machine: BODI/Bairuize
8. Human Machine Interface (HMI): Weilun Tong
9. PLC: Mitsubishi
10. AC contactor: Schneider
11. Air switch: Schneider
Cleaning products
