
Product Introduction: Battery Aluminum Shell Cleanliness Cleaning Line
The battery aluminum shell cleanliness cleaning line is a specialized cleaning equipment designed for battery aluminum shells. Its main task is to remove various dirt and residues on the surface of the aluminum shell through a series of efficient cleaning processes to ensure that the cleanliness of the aluminum shell meets the standards for production or use.
In the battery aluminum shell cleanliness cleaning line, multiple cleaning methods are usually integrated to achieve perfect cleaning results. Firstly, ultrasonic cleaning is an important part of it. The ultrasonic energy generated by high-frequency vibration can form tiny bubbles in the cleaning solution, which continuously expand and contract under the action of sound waves. This process generates strong impact force, effectively removing dirt and grease from the surface of the aluminum shell.
In addition to ultrasonic cleaning, high-pressure water flow cleaning is also a common cleaning method. High pressure water is sprayed onto the surface of the aluminum shell through a specialized nozzle, and the impurities and residues attached to the aluminum shell are washed away by the high-speed water flow. This cleaning method can penetrate into the small gaps and uneven surfaces of the aluminum shell, ensuring comprehensive and thorough cleaning.
In addition, chemical solvent cleaning is also one of the commonly used methods in the cleanliness cleaning line of battery aluminum shells. Specific chemical solvents can dissolve and decompose oil stains and residues on the surface of aluminum shells, thereby achieving the purpose of cleaning. These chemical solvents usually have the characteristics of high efficiency and environmental friendliness, and will not corrode or damage the aluminum shell.
The purpose of the battery aluminum shell cleanliness cleaning line is not only to improve the cleanliness of the aluminum shell, but also to ensure the quality and performance of the battery. The cleaned aluminum shell can remove surface dirt and residue, reduce the risk of internal short circuit and corrosion of the battery, and improve the safety and reliability of the battery. Meanwhile, the efficient and automated features of the cleaning line can significantly improve production efficiency, reduce labor costs, and bring higher economic benefits to the battery manufacturing industry.
In summary, the battery aluminum shell cleanliness cleaning line is an efficient and comprehensive cleaning equipment. It uses various cleaning methods such as ultrasonic waves, high-pressure water flow, and chemical solvents to ensure that the cleanliness of the battery aluminum shell meets the standards, thereby improving the quality and performance of the battery and providing reliable guarantees for the battery manufacturing industry.
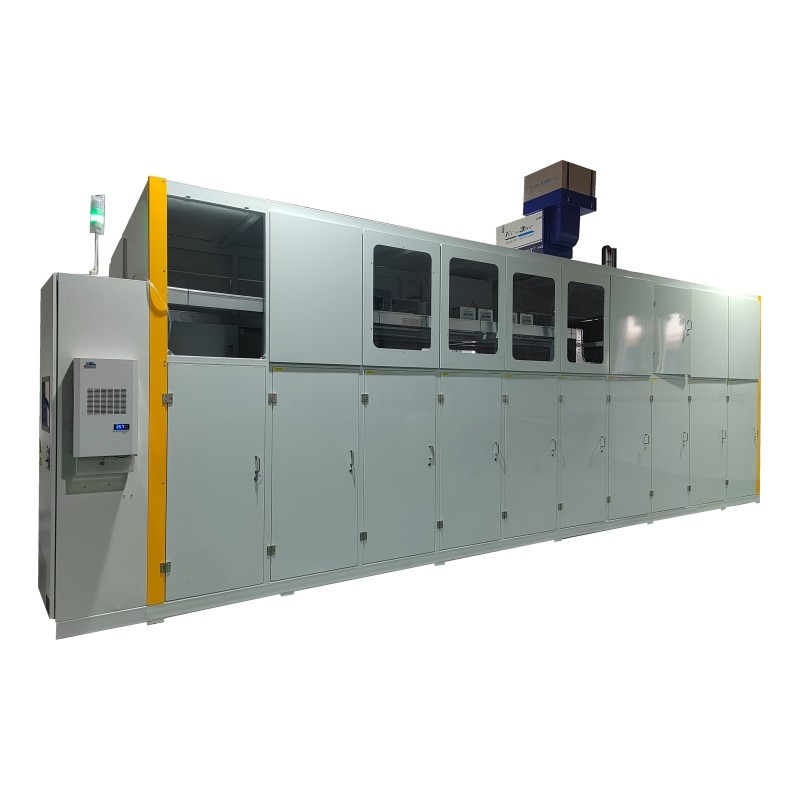
1、 Equipment cleaning requirements:
Realize particle size cleaning, drying, and cooling of cylinder components
1. Particle size requirement: Metal particle size ≤ 200 μ m
2. Meet the cleanliness requirements of the product, and ensure that the equipment and fixtures do not cause secondary scratches, bumps, or deformation due to squeezing on the surface of the parts
3. Drying requirements: The surface of the parts should be dry without any dripping water residue or visible water stains
4. Beat requirement: CT180S/basket
5. Processing capacity: 45 pieces/basket
2、 Equipment cleaning process flow:
Loading → 1 # ultrasonic cleaning → 2 # ultrasonic cleaning → 3 # ultrasonic rinsing → 4 # ultrasonic deburring cleaning → 5 # spray cleaning → 6 # flow ultrasonic cleaning → 7 # flow ultrasonic cleaning → 8 # vacuum drying → unloading
Cleaning process transfer: automatic truss robotic arm transfer
3、 Electrical Style:
1. Distribution panel: installed on the equipment body
2. Operation panel: installed on the electrical cabinet or cantilever mounted
3. Programmable Logic Controller (PLC): Mitsubishi/Siemens
4. Human computer interface (touch screen): Weilun
5. Operation mode: manual/automatic switching between each other
6. Operating interface: Chinese
7. Other control components in the distribution cabinet, such as air switches and contactors, use Schneider brand products
8. External sensor brand: Omron SICK、 Yifumen, Barufu, etc
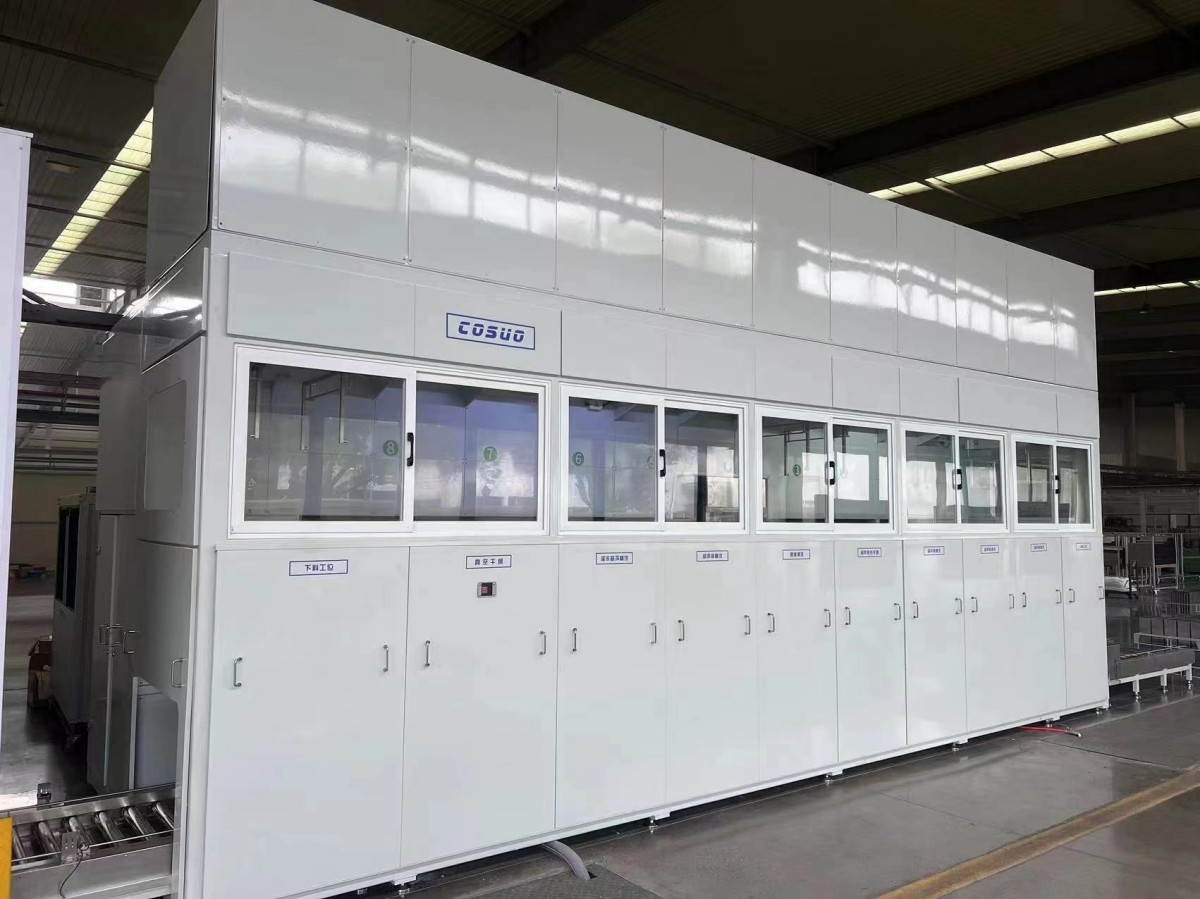

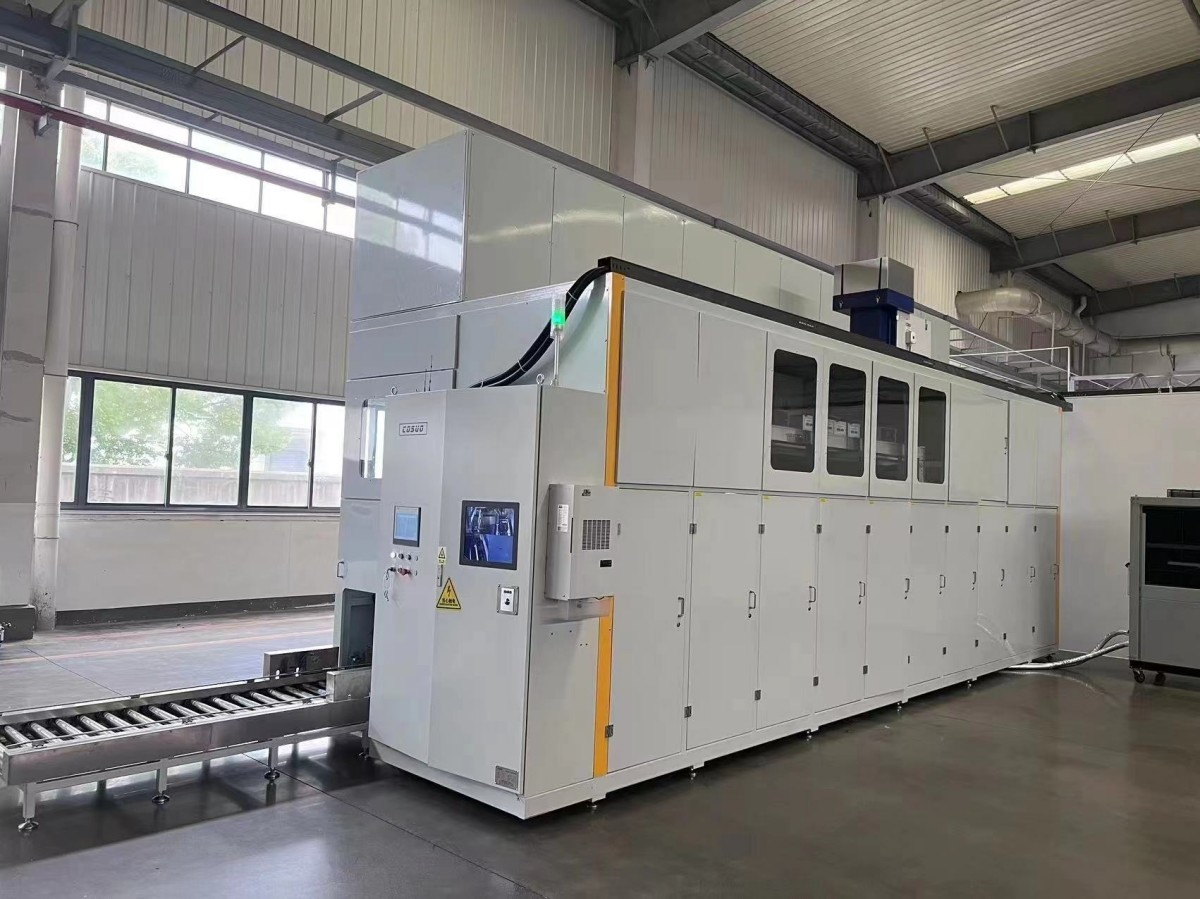
4、 Equipment material and exterior:
The equipment rack and surface cover plate are made of carbon steel material welded and coated, while the parts in contact with water such as the cleaning room, liquid storage tank, and pipeline are made of SUS304 material. The surface coating color of the equipment is specified by the customer or our company's standard color RAL9010
5、 Equipment installation conditions:
1. The size of the entire equipment is approximately 12000 * 2500mm
2. Equipment power supply: 3-phase 380V200KW (installed power)
3. Equipment drainage: 2-inch pipeline, manual discharge
4. Equipment connected to air: Compressed air pressure ≥ 0.5MPa, with a Ø 12 air pipe connected to an independent intake
6、 Equipment delivery time and installation and commissioning:
1. Equipment delivery time: 3.5 months after the contract takes effect
2. Installation and debugging
3. After the equipment arrives at the designated location of Party A, Party A shall notify Party B by phone or email and agree on the installation time
4. After the personnel of Party B arrive at the site of Party A, they shall unpack in the presence of both parties' personnel
5. The specific work of equipment positioning and primary side water inlet and power inlet shall be arranged by Party A, and Party B personnel shall be responsible for cooperation and guidance
6. The installation and commissioning work after the equipment is in place shall be the responsibility of the personnel of Party B. The required tools shall be provided by Party B, and Party A shall provide assistance if necessary.


7、 Equipment acceptance and training:
1. Equipment acceptance is divided into pre acceptance and final acceptance
2. Pre acceptance of equipment
3. Conducted at the factory of Party B. When the equipment is completed and meets the pre acceptance conditions, Party B shall notify Party A by phone or email and agree on the time and process of pre acceptance.
8、 Acceptance criteria:
1. The equipment configuration, technical specifications, and purchased brand meet the requirements of the technical agreement
2. The cleaning and drying effects of the parts meet the product requirements
3. The operation process of the cleaning machine is stable and logically reasonable
4. The cleaning cycle meets the requirements of the technical agreement
After the pre acceptance is completed, both parties shall sign the pre acceptance report. If there are rectification items involved, they shall be reflected in the pre acceptance report, and the rectification time shall be agreed upon. After the rectification is completed, Party B shall confirm the rectification items again through photos, videos, and other means.
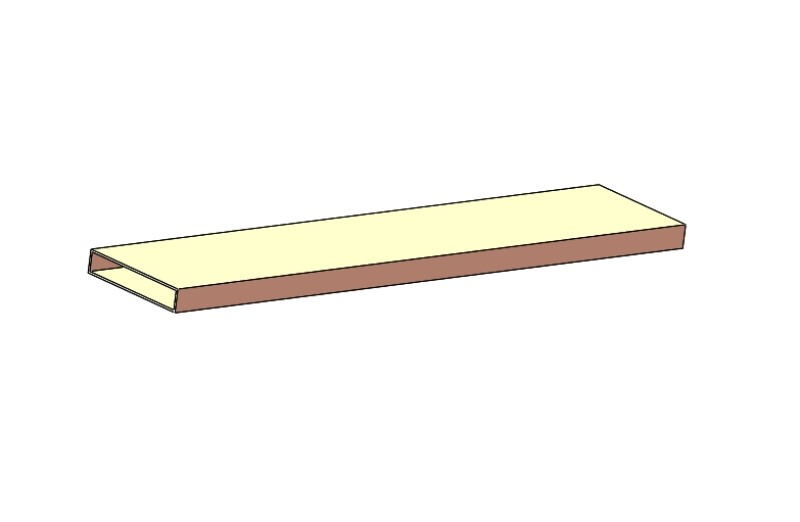
COSUO is committed to the research and development of ultrasonic deburring and ultrasonic cleaning equipment. Our existing products include ultrasonic deburring machines, ultrasonic cleaning equipment, ultrasonic cleaning machines, water-based ultrasonic deburring systems, hydrocarbon ultrasonic cleaning machines, fully automatic ultrasonic and high-pressure spray washing and drying equipment, etc. The COSUO brand creates the future!
Kesuo was founded in February 2008 and is an experienced manufacturer of high-precision ultrasonic deburring and cleaning equipment with advanced technology in the domestic industry. Adopting Japan's groundbreaking technology - wide area simultaneous multiple wave ultrasonic technology, the equipment's working ultrasonic intensity can reach more than ten times that of commonly used cleaning ultrasonic equipment in China. The core components of the equipment are all imported from Japan, and the whole machine is meticulously crafted with excellent performance. At the same time, we also use advanced ultrasonic core components from Germany, the United States, and other countries to provide customers with a wider range of choices.
Koso ultrasonic equipment can efficiently remove small burrs on the surface and inner cavity of precision components, micro holes, blind holes, pipelines, and other complex structures in batches, without damaging the surface of the components. Widely used in high-end fields of precision manufacturing industries such as automotive, medical, electronics, machinery, aerospace, and military, with strong universality.
In addition to providing various standard models, Kesuo can also customize multi slot or specially designed large-scale equipment according to customers' different needs. It can seamlessly connect with customers' automated production lines as needed, and fully automate and complete the deburring or cleaning process of components on the production line with high quality.
COSUO is committed to the research and development of ultrasonic deburring and ultrasonic cleaning equipment. Our existing products include ultrasonic deburring machines, ultrasonic cleaning equipment, ultrasonic cleaning machines, water-based ultrasonic deburring systems, hydrocarbon ultrasonic cleaning machines, fully automatic ultrasonic and high-pressure spray washing and drying equipment, etc. The COSUO brand creates the future!
Your satisfaction, my pursuit! We warmly welcome you to visit our company for inspection and negotiation, or to inquire by phone or letter!